You should probably grab a copy of Damian Harty's book, The Multibody Systems Approach to Vehicle Dynamics, as should I!
I'm pretty bad at the theoretical side of the Solver but when I'm given the time I can make it do what I need. Here's some nice curves showing parking efforts on concrete and on a greased plate. Black is ADAMS, orange and brown is test. The weird spike in the test data is due to bending in the tie rod we think.
https://www.mediafire.com/convkey/2247/ ... 0xu36g.jpg
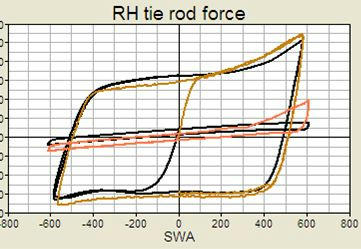