
http://racingtech.wordpress.com/2012/04 ... e-problem/
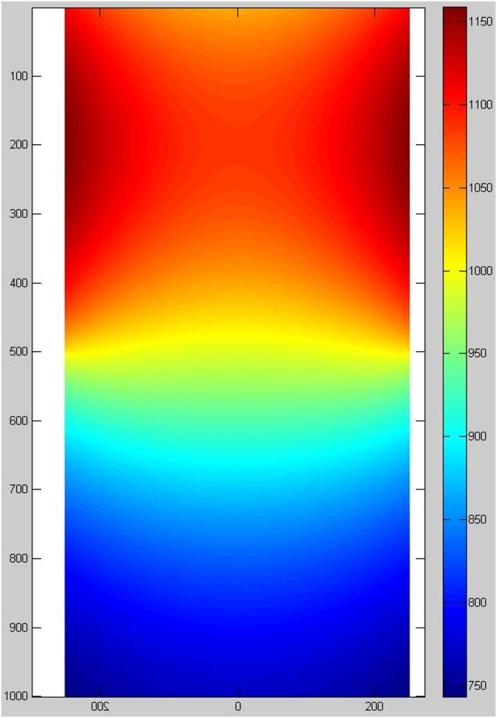
Yes, those assumptions are only temporary.riff_raff wrote:rough_wood,
I can't really comment on your math model because I don't have any expertise in this area. But with regards to carbon-carbon material properties there are a few peculiar issues to consider. As others noted, the thermal conductivity and Mu can vary with temperature. I also understand that thermal conductivity can vary with respect to lateral/transverse/longitudinal directions.
CRC materials also have definite temperature limits due to oxidation. The number I recall seeing is about 1500degF, but I don't have any data for current F1 brake materials.
Lastly, since this seems to be related to an engineering undergrad study, I'd recommend that you try contacting the racing brake manufacturers (Brembo, AP, etc.) and see about getting them to support your efforts. What you are attempting to do is quite ambitious, and I would imagine creating such an analytical model is beyond what the racing brake suppliers would typically attempt. They don't have the manpower or financial resources for such efforts.
Regards,
riff_raff
rough_wood,rough_wood wrote:.......As far as the temperature, they are below failing temperatures in carbon carbon heat shielding on re entry vehicles, however I don't know maximum temperatures of brakes. Another thing to note, is it's still just a slab and I assumed a duty cycle of 3 G braking since for now the model is treated as steady state.......
No man thanks for your input. Keep it comin.riff_raff wrote:rough_wood,rough_wood wrote:.......As far as the temperature, they are below failing temperatures in carbon carbon heat shielding on re entry vehicles, however I don't know maximum temperatures of brakes. Another thing to note, is it's still just a slab and I assumed a duty cycle of 3 G braking since for now the model is treated as steady state.......
Sorry if it's not helpful to your modelling, but just a couple more comments about CRC brake materials:
There are two basic types of commercial CRC friction materials, PAN based and pitch based. In general, the PAN based materials tend to have better structural properties, and the pitch based materials tend to be tougher. I believe both types are used for aircraft brakes, but I don't know about racing brakes.
When both the rotor and pads are made from CRC, it presents a different wear situation than that existing in conventional metal brake rotors. With CRC pads and rotors, both are subject to significant wear. The section and mass properties of the CRC rotor may change appreciably over the course of a race. Many years ago when CRC brakes were first introduced to F1 racing the rotor wear rate was quite high, but I don't know what it currently is. Reduced thermal mass and section thickness will affect both heat transfer and mechanical stress in the rotor.
Just more things to consider in your brake model.![]()
slider