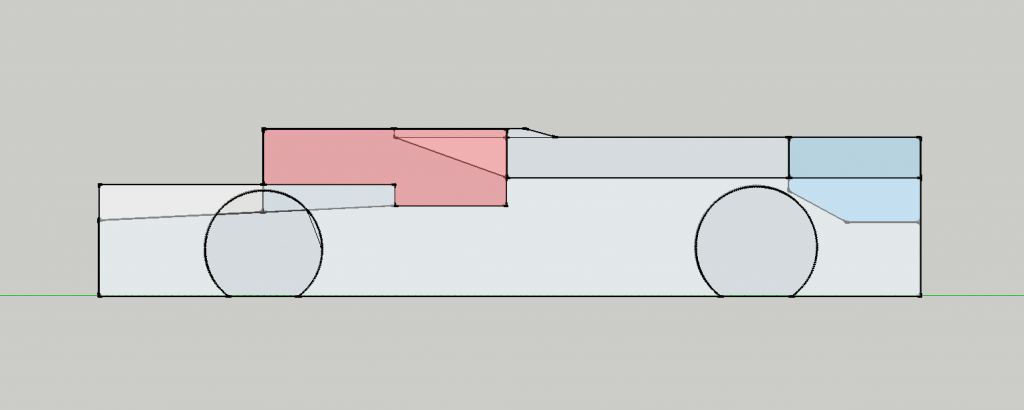
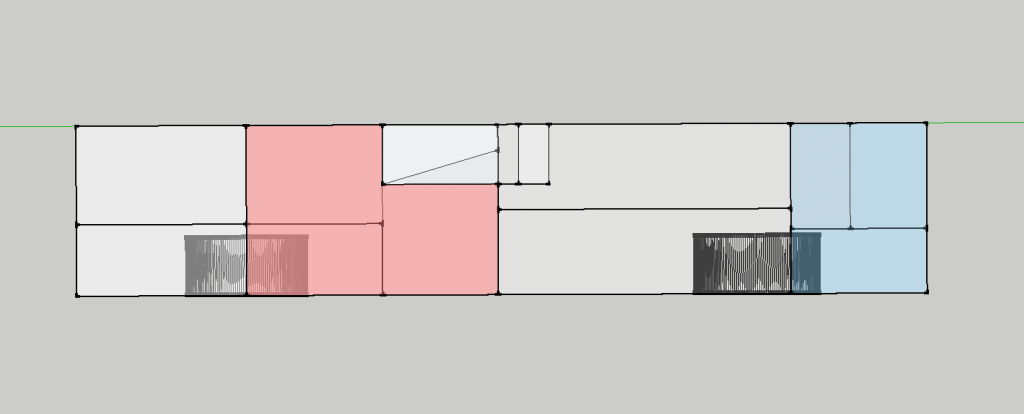
About making LMP1 look alike models, it's not a problem for me. However it would be interesting to see what happens with more open regulations (i imagine LMP cars with actual front wings, coke bottles rear ends,...)
Do you mean to change the boxes we have now, or to add further rules from the LMP1 rulebook, but modify those rules to allow larger zones for bodywork?CAEdevice wrote:I welcome any proposal in favor of realism (K3.5, K3.6), but I would agree the proposal to make the LMP1 based rules less stringent, for example working on the dimensions of the regulated areas.
Yep, the parts are meant to represent the entire volumes occupied by the suspension members as they move. I will include the actual suspension parts separately in the next release, keeping in mind that these parts have no bearing at all on regulations, they are only there for CFD purposes.CAEdevice wrote:One question about the CAD template: does the suspension geometry represent the volume occupied during the movement? In the final version would be useful to have also the nominal geometry of the suspension in order to correctly simulate the flow.
I am leaning towards leaving 3.7 out, since the front suspension already has to be covered from the front and top. With the added constraint of K3.7 it just makes a building a car with a front wing more difficult in terms of meeting the regulations.CAEdevice wrote:Hi, what about the proposal K3.5, K3.6, K3.7?
I think that if all the proposal will be applied some ideas could not be realised, but if none of them will be confirmed, cars will look like airplanes...
I would agree to mantain at least K3.7.
I just wanted to highlight this post from earlier on - while I can't guarantee we will have time to do this, we would like to supply some optional basic parts to make things easier. Most likely a central set of bodywork forming the nose /tub / engine cover, and fenders to cover the front and rear wheels, as a minimum.eyalynf1 wrote:My difficulty has been having time to complete the modeling alone. So from a purely selfish stand point, I'd like to see the modeling effort required reduced so that I can get to the CFD part more quickly.
For me, this would mean more spec parts, with customization limited to 1 or 2 handfuls of areas. Say a box between the wheels on the sides, a box in front of the front wheels, behind the back wheels, and above the back box. A bit limiting, yes, but if the point is to disseminate and develop CFD software, skills, and use, then getting competitors to the CFD but faster would seem logical.
Yes, this rule is a bit vague but you have the right idea. This might change if we can find a better way to describe this.MadMatt wrote:I am a bit confused at rule K2.5:
"From any other viewing angle ahead of the rear wheel centerline which is above and to the side of the car, no part of the rear suspension volumes may be visible."
Does that mean the rear suspension parts cannot be seen from a person standing in front of the rear axle line no matter where?
There is a single plane anywhere between 0 and 300mm rearward of the front face (this has been changed to read between 700mm and 1000mm forward of the front wheel CL). You decide exactly where this plane is, and then the area of the intersection(s) at that plane are measured. We can probably change it to just "at 300mm rearward" rather than "between 0 and 300mm rearward".MadMatt wrote:Also another question about K3.1. What happens in the area from 0 to 300mm behind the forward most surface of the control volume? The crash structure has to expend but I read:
"At a plane located between 0 and 300mm rearwards of the forwardmost face of the bodywork volume, the intersection with the front crash structure forms one or more closed shapes. Excluding any areas more than 300mm from the car centerline, the shape(s) must be at least 16000mm^2 in total area."
However it is impossible to have a surface of 16000mm^s at a plane 1mm ahead of that forward most surface since the crash structure is just starting. Is it not only at 300mm that there must be a minimum of 16000mm^s of surface for that crash structure?
There is a vague rule about there being a plausible path for air to flow from the inlet to the outlet (but this internal path doesn't need to be modeled). It's at the end of K4.2.CAEdevice wrote:About the "box dimensions": i would reduce the lenght of the frontal extension of the cooling inlets (1000mm >>> 900/800mm) and I would add this rule: "no bodywork could be placed into the volume generated by a blend between the cooling inlet and outlet surface. Sorry if there is something like this that I have not noticed yet.
Correct, at the moment this is allowed. I think it's very likely we will add a rule stating "when intersected with a plane normal to the X-axis, must form a single, uninterrupted line entirely visible from below" applying to bodywork in the diffuser area, unless anyone has a good reason we should leave it like it is.CAEdevice wrote:Last point: at the moment it seems to me that "double" or "overlapped" diffuser are allowed, I'm I right?
I'll reduce this to 10mm, but anything less than that would probably be too small. Keep in mind that very thin parts can cause problems at the meshing stage. A semi-circular leading edge is fine, I'll add an image to the rulebook to guide this.MadMatt wrote:K1.4: So any part cannot be less than 20mm at any point? Is it possible to start with a square shape of 20mm thickness and then radius it to get a trailing edge? 20mm is quite big in my opinion. Would it be possible to at least sharpen the leading edge as well so get don't get these horrible flat surfaces presented to the wind?
I take as an example a rear view mirror mount. 20mm thick is not pretty when it should be 3mm!
This isn't set in stone yet, but we will be building on what we used in 2013 and 2014, with some additions, such as simulated inlet and outlet surfaces. There will be moving wheels and a moving ground plane.MadMatt wrote:Following my question 2 messages above regarding the 20mm thickness, I would like to ask questions about the CFD methodology. How is it gonna be simulated?
- Moving wheels?
- Moving floor?
- Sea level conditions (air density, viscosity)?
- Air velocity?
As I am having a break from my laptime simulator project, I gave it a go at this one, and came up with a preliminary design. Eventho I won't put it straight into my CFD software to get a benchmark, it would be good to know what kind of car we are aiming to get.
Also will the rediator templates be provided?
Hi Matt, I think that with a C Group style it would be difficult to have a good balance (too much DF on the rear axle, because the diffuser area is concentrated on the rear axle).MadMatt wrote:Thank you! Much clearer nowI guess there will be 3 kinds of designs (to to mention mixes of 2 or the 3):
- Group C type
- LMP type
- F1 type
I think it will be very interesting to see who choose what and how far people go with their design. I agree that the design is quite restrictive, but at least it removes possibilities that would cause too big differences in the results, so its good!