
I was fascinated by this grid:
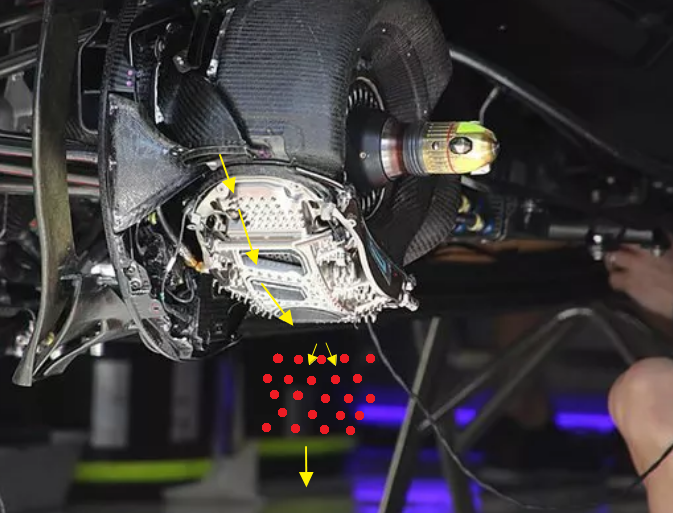
I suspect RB has done a thorough analysis of this behaviour and the optimization of the spacing and pin shape. These circular rods seem to have the most cooling performance.
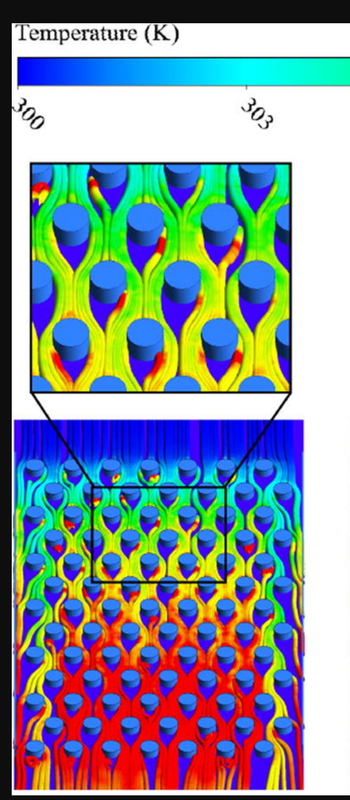
Pins can be used. Many LED fixtures come with pins. Depending on what you want whether fouling, structural etc.
Is it possible that the pins are actually structural to prevent the outer shell of the cake tin from deforming and restricting the airflow?Henk_v wrote: β02 Mar 2023, 23:59I design heat exchangers for a living. I hope I'm not confused...
I am not at all saying fins are terrible. They are just not the best for radiative cooling. Fins are great if the limit of heat exchange is in the thermal conductivity of the exchanger. They provide a low resistance way of exposing area and a large conduction path.
If you look better at radiators, you'll discover that high performance radiators are often a hybrid between pin and fin. The fins are perforated and skewed to make many small fins to mix the airflow and break the boundary layer.
In aluminium the thermal conductivity is not a limiting factor and pins can(can!) be effective in keeping boundary layers at bay and mixing the airflow at the cost of some additional resistance.
Air is terrible at absorbing radiation. The radiation of the sun needs about 16 km of atmosphere and some stuff in it to be attenuated enough to make earth livable,
Absorbing the heat radiation with another body with a low emissivity and convectively transferring that heat to the air can be a great way to make the heat exchange to the air more effective and could potentially keep the shroud cooler. A cooler shroud may give an opportinity to use lighter non-metallic composites near it reducing weight (allthough I realise that is quite an hypothesis)
Well in reality in the feild. Fins are more efficient. It seems you do design in theory or for research. You are talking about radiation only.Henk_v wrote: β02 Mar 2023, 23:59I design heat exchangers for a living. I hope I'm not confused...ringo wrote: β02 Mar 2023, 22:22Maybe you are confusing what is happening. The convection is of the air blowing past the pins.Henk_v wrote: β02 Mar 2023, 21:34I have a shoe here fearing for his future. I hope more pictures arrive...
Regarding the pins on the caliper; at the temperatures the brakes run, heat exchange by radiation can exceed convective heat exchange. Fins are terrible at radiating as most of the surface radiates towards the neighboring fins. I can imagine the shroud being of conductive material and having pins too. The pin spacing seems to imply this. Heat will then be transferred to the shroud by radiation and is convectively transferred to to the cooling air by the shroud pins. This could mean the shroud runs a bit cooler, which may be a desirable effect.
Radiative heat transfer usually has to do with light emission, such as fire etc. Once the view of that light or radiation, be it IR or whatever is blocked by a body then you are mostly depending on convection to transfer heat behind the shadow of that body.
Fins are not terrible for heat transfer. That's why radiators in most applications have fins and not studs.
Both have their strengths and weaknesses, usually with studs, it's for mechanical reasons why they are selected.
I am not at all saying fins are terrible. They are just not the best for radiative cooling. Fins are great if the limit of heat exchange is in the thermal conductivity of the exchanger. They provide a low resistance way of exposing area and a large conduction path.
If you look better at radiators, you'll discover that high performance radiators are often a hybrid between pin and fin. The fins are perforated and skewed to make many small fins to mix the airflow and break the boundary layer.
In aluminium the thermal conductivity is not a limiting factor and pins can(can!) be effective in keeping boundary layers at bay and mixing the airflow at the cost of some additional resistance.
Air is terrible at absorbing radiation. The radiation of the sun needs about 16 km of atmosphere and some stuff in it to be attenuated enough to make earth livable,
Absorbing the heat radiation with another body with a low emissivity and convectively transferring that heat to the air can be a great way to make the heat exchange to the air more effective and could potentially keep the shroud cooler. A cooler shroud may give an opportinity to use lighter non-metallic composites near it reducing weight (allthough I realise that is quite an hypothesis)
Yes i suspect this is the reason. Something rests on those pins and air possibly flows through that cavity.djos wrote: β03 Mar 2023, 01:22Is it possible that the pins are actually structural to prevent the outer shell of the cake tin from deforming and restricting the airflow?Henk_v wrote: β02 Mar 2023, 23:59I design heat exchangers for a living. I hope I'm not confused...
I am not at all saying fins are terrible. They are just not the best for radiative cooling. Fins are great if the limit of heat exchange is in the thermal conductivity of the exchanger. They provide a low resistance way of exposing area and a large conduction path.
If you look better at radiators, you'll discover that high performance radiators are often a hybrid between pin and fin. The fins are perforated and skewed to make many small fins to mix the airflow and break the boundary layer.
In aluminium the thermal conductivity is not a limiting factor and pins can(can!) be effective in keeping boundary layers at bay and mixing the airflow at the cost of some additional resistance.
Air is terrible at absorbing radiation. The radiation of the sun needs about 16 km of atmosphere and some stuff in it to be attenuated enough to make earth livable,
Absorbing the heat radiation with another body with a low emissivity and convectively transferring that heat to the air can be a great way to make the heat exchange to the air more effective and could potentially keep the shroud cooler. A cooler shroud may give an opportinity to use lighter non-metallic composites near it reducing weight (allthough I realise that is quite an hypothesis)
F1 radiators don't use fins. They use micro tubes. This is quite analogous to a stud except the "fluid" inside the stud, is just heat flow .ringo wrote: β03 Mar 2023, 03:41Well in reality in the feild. Fins are more efficient. It seems you do design in theory or for research. You are talking about radiation only.Henk_v wrote: β02 Mar 2023, 23:59I design heat exchangers for a living. I hope I'm not confused...ringo wrote: β02 Mar 2023, 22:22
Maybe you are confusing what is happening. The convection is of the air blowing past the pins.
Radiative heat transfer usually has to do with light emission, such as fire etc. Once the view of that light or radiation, be it IR or whatever is blocked by a body then you are mostly depending on convection to transfer heat behind the shadow of that body.
Fins are not terrible for heat transfer. That's why radiators in most applications have fins and not studs.
Both have their strengths and weaknesses, usually with studs, it's for mechanical reasons why they are selected.
I am not at all saying fins are terrible. They are just not the best for radiative cooling. Fins are great if the limit of heat exchange is in the thermal conductivity of the exchanger. They provide a low resistance way of exposing area and a large conduction path.
If you look better at radiators, you'll discover that high performance radiators are often a hybrid between pin and fin. The fins are perforated and skewed to make many small fins to mix the airflow and break the boundary layer.
In aluminium the thermal conductivity is not a limiting factor and pins can(can!) be effective in keeping boundary layers at bay and mixing the airflow at the cost of some additional resistance.
Air is terrible at absorbing radiation. The radiation of the sun needs about 16 km of atmosphere and some stuff in it to be attenuated enough to make earth livable,
Absorbing the heat radiation with another body with a low emissivity and convectively transferring that heat to the air can be a great way to make the heat exchange to the air more effective and could potentially keep the shroud cooler. A cooler shroud may give an opportinity to use lighter non-metallic composites near it reducing weight (allthough I realise that is quite an hypothesis)
I'm in oil and gas engineering for over 10 years. I don't specialize, i dabble in a lot of equipment design. Pin extended surface exchangers are much bigger. Less heat exchange simply down to less surface area. I am sure you can work out some surface area calcs and see for yourself. Also there are some phenomena in reality that you are limited by such as fin/stud tip temperatures.
Studs/pins are usually used over fins because they are more resistant to fouling and corrosion and theyre mechanically stronger. 90% of the time we use fins for convective heat exchange. Studs are special case. And explains why you will see most radiators, especially in automotive applications having fins. Case in point the same F1 radiators. Convection between air and metal surface.
And again There is mostly convective heat exchange in that area on the brake. Not radiation. With radiation you usually have more than enough heat flux to not need to use fins or pins, the bare surface is sufficient.
Microtubes are used because they are better for heat exchange. Please read the link I shared: https://www.racecar-engineering.com/news/micros-scope/PlatinumZealot wrote: β03 Mar 2023, 04:16If i recall the microtubes are for aerodynamic reasons not heat exchange reasons. At 200mph drag and fouling is a bigger issue for the fins so the tubes are the best compromise.
Yes, while I don't have any experimental evidence, I believe it is a good extrapolation to assume the "pins" are quite good for heat transfer (better than fins atleast). Likely less drag and more heat rejection, analogous to microtubes.PlatinumZealot wrote: β03 Mar 2023, 04:16
And coincidentally! This is the analogous to using pins on the caliper...
(get it? The microtubes are circular like the pins).
Another great innovation from RedBull?
I know about microtubes. And i read that article already.AR3-GP wrote: β03 Mar 2023, 04:23Microtubes are used because they are better for heat exchange. Please read the link I shared: https://www.racecar-engineering.com/news/micros-scope/PlatinumZealot wrote: β03 Mar 2023, 04:16If i recall the microtubes are for aerodynamic reasons not heat exchange reasons. At 200mph drag and fouling is a bigger issue for the fins so the tubes are the best compromise.
https://www.racecar-engineering.com/wp- ... 6/Fig3.jpg
https://www.racecar-engineering.com/wp- ... 6/Fig4.jpg
No. A fin or a stud is a extended surface. They go onto the tube carrying the fluid. There is no "fluid inside a stud" scenario. A stud by definition is something attached to the tube. In the case of a microtube, it's a bare surface, which as I said earlier example in most cases with radiation the tubes have no extended surface. For microtube it's convection with no extended surface. I hope this provides clarity.AR3-GP wrote: β03 Mar 2023, 03:50
F1 radiators don't use fins. They use micro tubes. This is quite analogous to a stud except the "fluid" inside the stud, is just heat flow .
Fantastic article here:
https://www.racecar-engineering.com/news/micros-scope/
As a fellow ignorant, I think we can make a basic assumption that the pins are for cooling. Whether fins would be better? I'd like to think they evaluated this; however, they are not infallible so...dialtone wrote: β03 Mar 2023, 05:22As an ignorantβ¦ if pins were more efficient they would be used in electronics which instead universally uses fins with forced air. There is hardly anything as power dense as modern CPUs and GPU which develop over 400W of power in barely above 1cm^2. Surface area when forced air is involved is fins, probably pins when no forced air?
Edit: micro tubes could be different though to be honest as likely cost could become the reason there. I can easily imagine thick micro tubes to be very efficient surface-wise, especially if they run coolant inside which has higher heat exchange coefficient.
Yes correct. Fins are used extensively.dialtone wrote: β03 Mar 2023, 05:22As an ignorantβ¦ if pins were more efficient they would be used in electronics which instead universally uses fins with forced air. There is hardly anything as power dense as modern CPUs and GPU which develop over 400W of power in barely above 1cm^2. Surface area when forced air is involved is fins, probably pins when no forced air?
Edit: micro tubes could be different though to be honest as likely cost could become the reason there. I can easily imagine thick micro tubes to be very efficient surface-wise, especially if they run coolant inside which has higher heat exchange coefficient.
Agree, they evaluated many things outside of just theoretical heat transfer rates. With fins, the flow has to come from a certain direction to go between the fin rows. Studs can facilitate flow in all kinds of directions. Also from the caliper it looks like they did not need many of the studs and it was maybe easier to fabricate that wide spacing compared to doing the same with a fin or rib.AR3-GP wrote: β03 Mar 2023, 05:37As a fellow ignorant, I think we can make a basic assumption that the pins are for cooling. Whether fins would be better? I'd like to think they evaluated this; however, they are not infallible so...dialtone wrote: β03 Mar 2023, 05:22As an ignorantβ¦ if pins were more efficient they would be used in electronics which instead universally uses fins with forced air. There is hardly anything as power dense as modern CPUs and GPU which develop over 400W of power in barely above 1cm^2. Surface area when forced air is involved is fins, probably pins when no forced air?
Edit: micro tubes could be different though to be honest as likely cost could become the reason there. I can easily imagine thick micro tubes to be very efficient surface-wise, especially if they run coolant inside which has higher heat exchange coefficient.