Suposing you don't have any problem chasis wise(can locate poits anywhere), you could make isosceles triangles, righ triangles, etc.
For example, in "old" f1 you could see very long arms at the rear, pointing forwards.
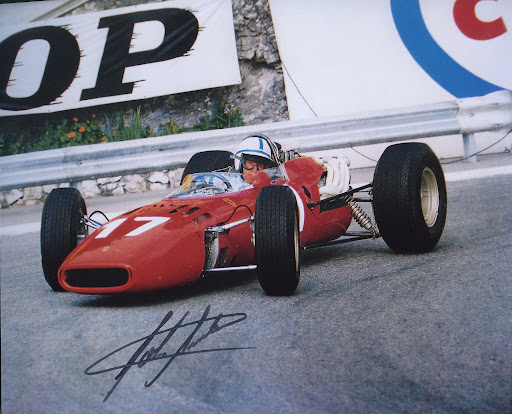
It seems that in this type would be easier to deal with the loads, but a long arm seems it could buckle.
Is there any reason to use(or avoid) any specific type?
Another thing I've seen is that the rear and front inner pivot points are joined(in the front suspension).
Like this:
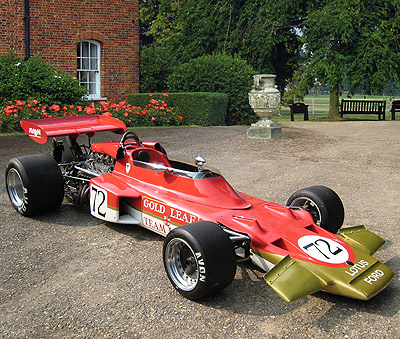
Why would you do that? To account for chassis deformation?
Here's another picture that shows long rear control arms, almost right triangle lower front wishbone with a long rear pivot control arm. We con also see a very "small" front upper wishbone.(used also as a lever for the coilover.)

Any input is welcomed!
bye bye

Caito.-
PS: Some nowadays cars. Generally speaking we can see in the rear right triangles with a long front control arm. In the front, the honda for example, has right angle wishbones, seems the bmw has them too.




