Its a common style of pushrod, and so too is its construction.
The pushrod is aero in cross-section where the gold titanium insert is bonded in and it tapers in cross-section towards the opposite end where the single ferruled and washered hole lies. Both top and bottom sections of profile converge towards the last 100mm where they become one.
The main area I wanted to study inside the pushrod was where the ti insert gets bonded in. I wanted to see the bolt securing arrangement, the glue films, and also if the interior of the pushrod had been prepared in any way prior to insert installation.
I also wanted to have a general closer look at the pushrods cross-sectional construction. From general interior, to the carbon fibre wall layer orientation.
The pushrod measures around 340mm x 65mm x 19mm.
The pictures below show how I sectioned it to display various areas I wanted a closer look at.
The titanium insert itself features yellow titanium nitrate(TiN) coating on all surfaces excluding the bond surfaces. These have been grit blasted after coating to improve mechanical grip, since TiN is low friction, grit blasting is important in bond areas.
Titanium nitrate coating eliminates galling, fretting, microwelding, and corrosion seizing so it is a useful process where such parts are concerned. Anti gall being important for threaded holes. This coating is also three times harder than chrome.
The coating is also extremely thin at around 3µm, so doesn't really effect dimensional accuracy.
Im sure you have all seen, or used gold coloured drill bits. This is the same coating, but instead used on an alloy steel in the case of drills. Its used for the above reasons.
Titanium Nitride (TiN) is the most common PVD(Physical Vapour Deposition) hard coating in use today where precision parts are concerned.
The opposite end of pushrod featured a basic two piece titanium washer and ferrule arrangement bonded into a drilled hole, they have been removed, and are not pictured.
The part is made up from many layers consisting of unidirectional carbon fibre and
twill weave.
Normally, four to seven layers of unidirectional are used, followed by a layer of twill to keep them in place, this is repeated however many times necessary.
If you look very close at the cross-section pictures, you can see that the top and bottom halves are bridged together with a narrow build up of splicing layers.
Since this is pre-preg, all the layers can be built together using a type of mandrel. Since I wasn't present when this was constructed I cannot say for sure how it was constructed. But I can take a guess having been in factories that make similar parts.
A steel male mandrel tool could have been used to build the layers up on. Once built, the mandrel would have been slid out and a tube style bladder inserted.
The assembly would then be placed into a female tool having top and bottom sections to allow part removal.
They are brought up to temperature and the bladder inflated.
Once cured, either with a clave, or heated tools the tools can be opened, and the parted removed. These tools often feature small 'gates' along the part line. These gates all enter side runners in the tool. Depending on setup, the operator may attach a vacuum line to this main runner to help evacuate excess resin. Sometimes, no vacuum line is used and the resin just flows out of its own accord.
Other times, a top and bottom section are made, and both halves bonded together to form the profile.
A foam core is also used sometimes. The layers are built up around this foam mandrel as with the steel mandrel. The assembly is then placed inside the female tool and the halves closed. Because of the slightly oversize foam inside, the layers have to compress in order for tool to close fully.
Pending on where you have the foam left oversize, you can compress more areas of the part than others once the tools close. This way, you can concentrate on areas where the most loads are at the planning stage.
The foam can also be washed out with a solvent once the part is cured, making it even lighter.
There are lots of ways as you can see. Some more suited to wetlay, and others benefiting from pre-preg methods where the operator can take their time laying up various sections around a mandrel, or into a tool with very little mess, or weave disruption.
Trimming is also very easy with pre-preg, and a part can even be built in a modular fashion if you like, where several sections of the part can be laid up in different jigs, and then all brought together in the final tool for the final cure.
This is one of the main differences between wet lay, and pre-preg, it gives the designer greater scope in terms of constructing the part prior to curing. This is not as easy with wet lay, as it can turn into a big mess pretty quick if its a complex part. You can also lose your weave structure very fast the more you work wet lay. This is not the case as much with pre-preg since it is like applying thick masking tape and it tends to stay where its put when warmed and worked into place.
Onto the pictures.
They are pretty much self explanatory. Ill talk a little about the last few macro shots of the ti insert, and its surroundings.
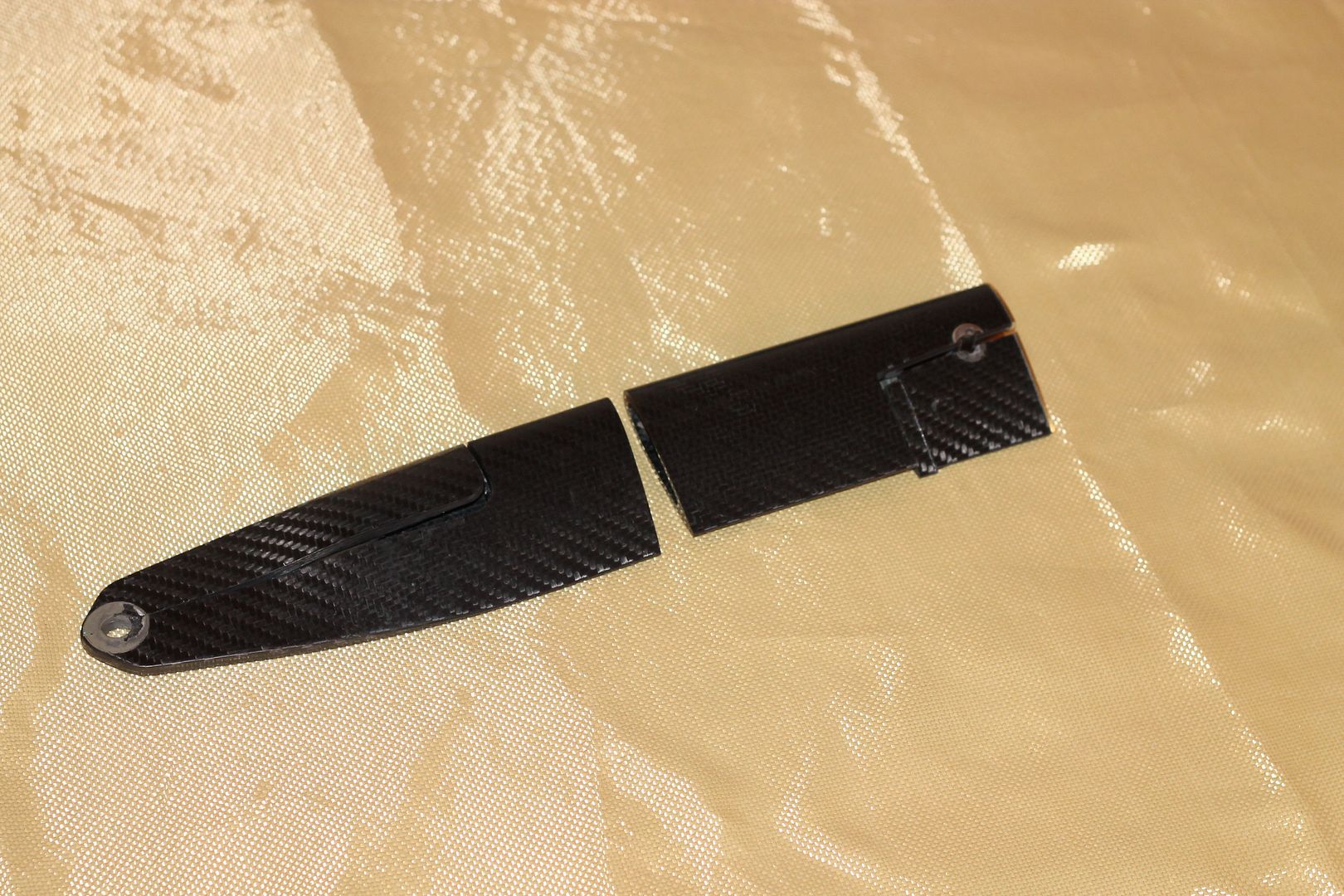





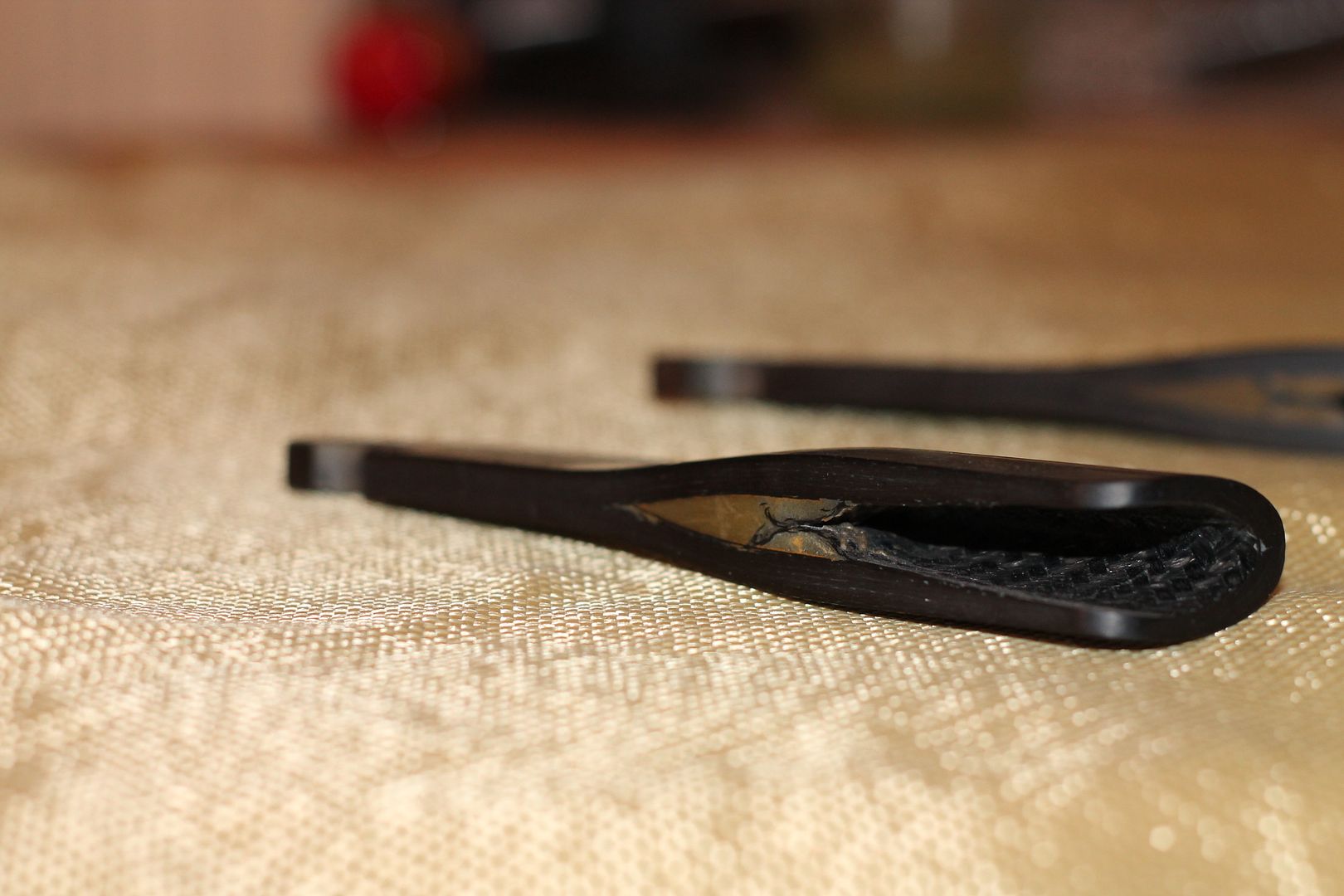
I polished up the inserts cross-section to make it all easier see,
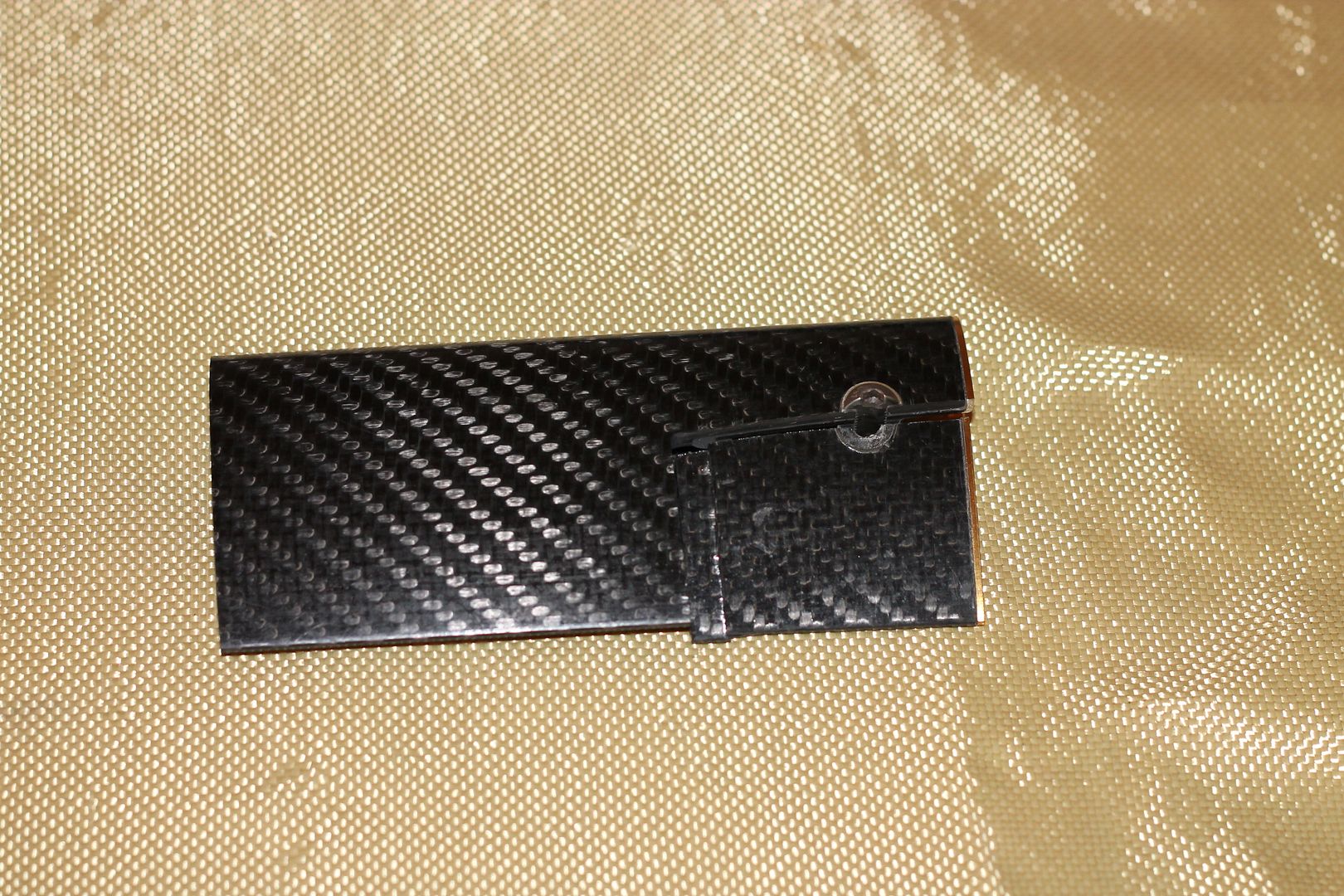

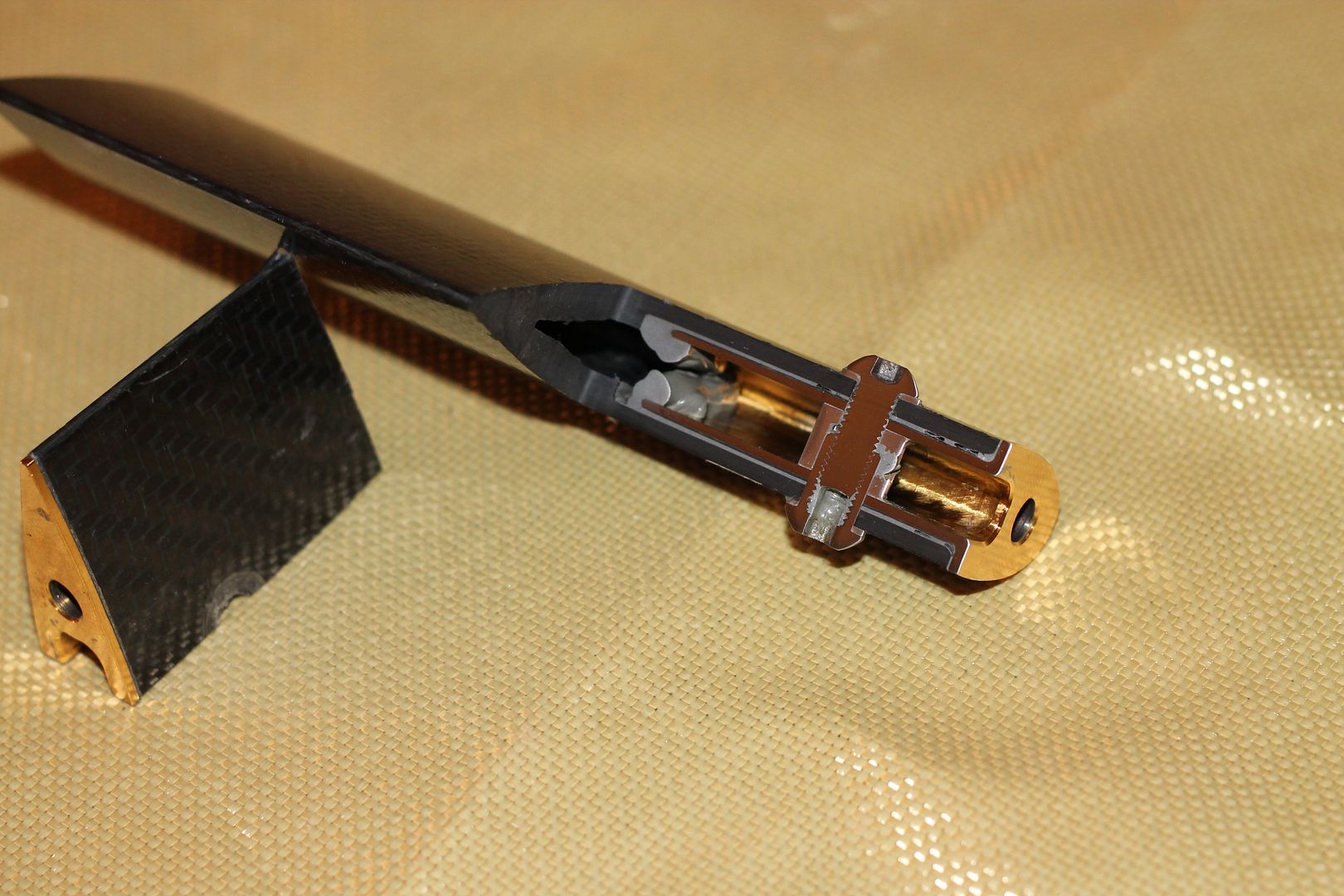
Interestingly enough, the insert fell out of its bonded position once the mechanical fixing was removed. No trace of bonding was present on the ti, it was completely smooth.
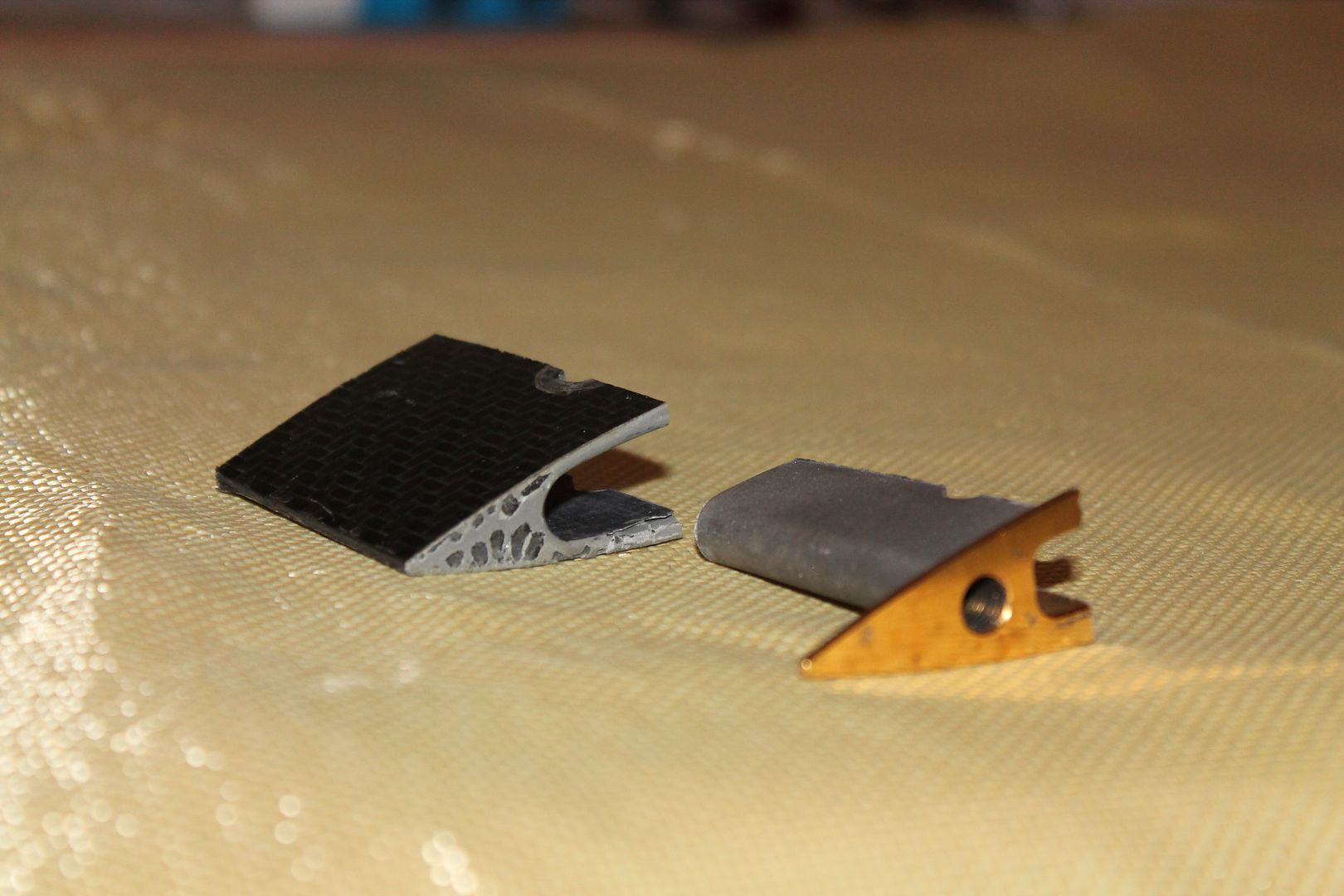
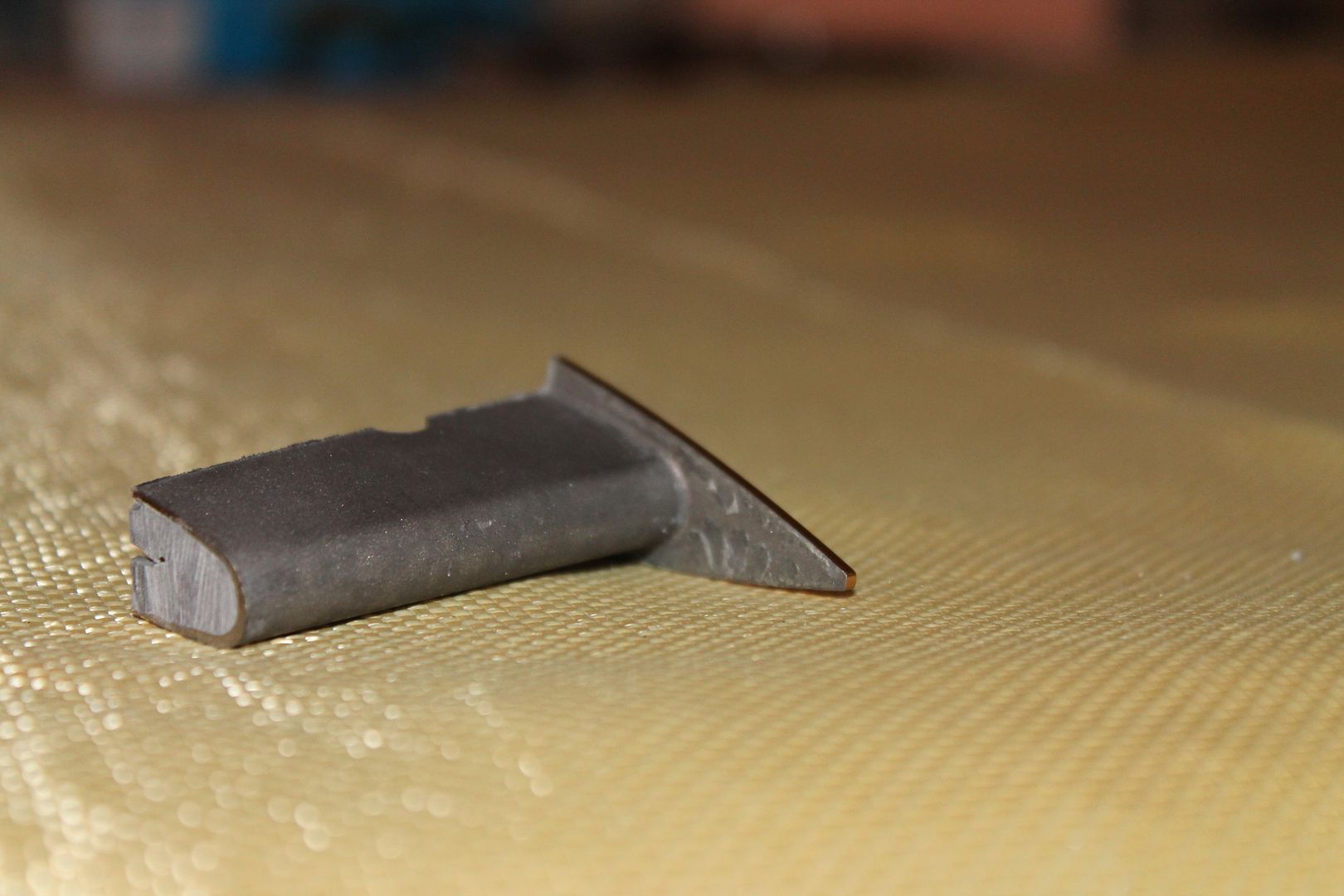
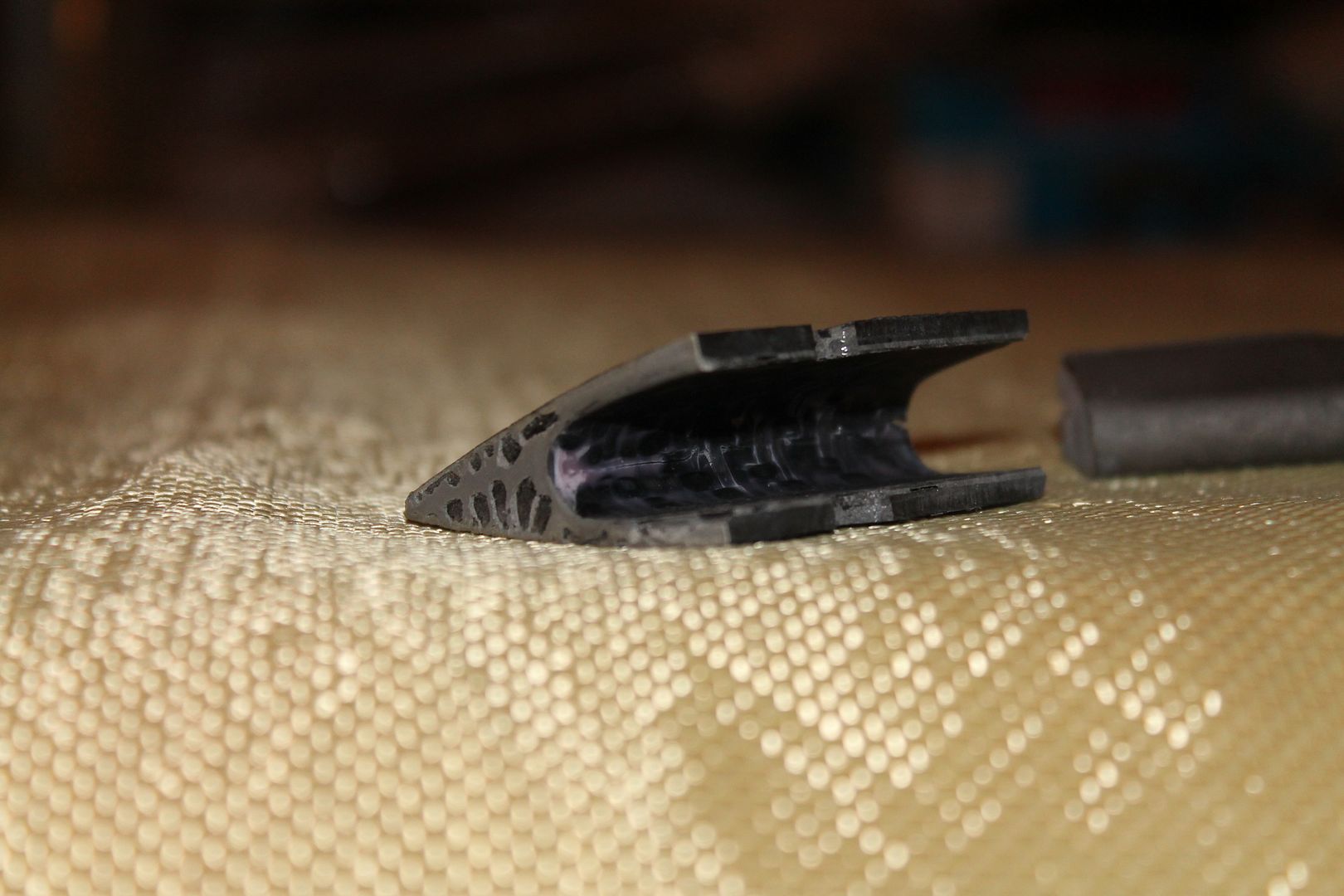
Here you can see the grit/media blasted finish of the ti insert.

Next, onto the macro shots of both the insert, and of the layers.
An important shot below,
Theres a lot going on here, so Ill mention the main parts.
From the top down,
The main bolt ( steel)
Washer (Aluminium)
Wall of pushrod (CF)
Epoxy adhesive
Thin layer of CF applied to ti insert before installing - !this is CF, and not GF!
Insert (Ti)
Spacer (Grit blasted Al)
Hex head insert nut (Steel)
You will also notice a threaded section in the side of the spacer.
From looking at other bonding procedures Im pretty this was used to both position spacer, and also for the pumping in of epoxy adhesive once the bolt was fitted and tightened enough to stop the epoxy flowing out under the bolt and nut heads.
If you look at the top and bottom of spacer where it joins the ti insert, you will notice a thin film of epoxy present, and also some surrounding the spacer itself.
Given that there are no traces of epoxy present like there would be if the insert was slid into place on a bed of epoxy, this further points to the application of epoxy via the side hole in spacer.
The spacer would have been machined a few thou less than the internal size of the ti insert. This slight undersize would allow enough room for epoxy to flow out very slightly at the top and bottom areas of spacer, which it did.
Once filled, the bolt was then tightened fully, completing the bond.
The ti insert also had its coating removed in the spacer bond area. This was carried out with what looks to be a file, or oxide paper.
One last point about the nut insert. You'll notice its not blind, meaning, its got an open hole passing through it. This is done for a few reasons.
It allows excess run-out epoxy adhesive to be removed.
It makes for a lighter nut.
It avoids hydraulic lock, where the epoxy would act as a seal between threads, and excess epoxy builds up in the blind hole, ahead of bolt end.
This has some nasty effects, from not allowing you to insert bolt fully, to swelling the insert.
This last one is the most dangerous, if the insert swells before final bolt torque is reached it can appear to be tight, but the bolt not actually in full tension at all.
The same theory applies to head studs and bolts. If you do not clean blind holes in block of oil or water, you will burst you block on tightening the studs, iron or Aluminium, hydraulics will cause it will pop.
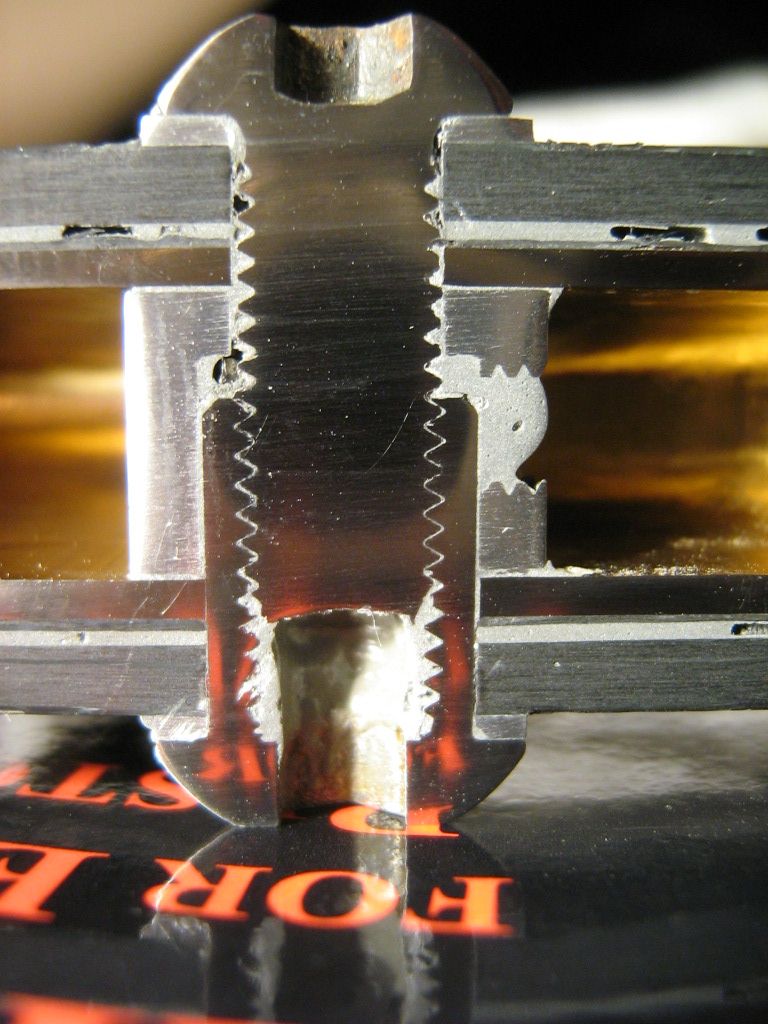


You can also see where the end of the CF profile was machined with an end mill to both clean up the irregular interior, and to also provide a perfect match and bond clearance for the ti insert.

Here, is a small piece cut off, showing the end of the machined pocket section, it extends about 5mm deeper than inserts length.

One thing that surprised me a little is the used of an end mill to mill the pocket. You would think a ball nose cutter would have left a smoother transition.
I guess it may not matter considering the force lines, but I still always hate to see sharp 90 degree transitions.
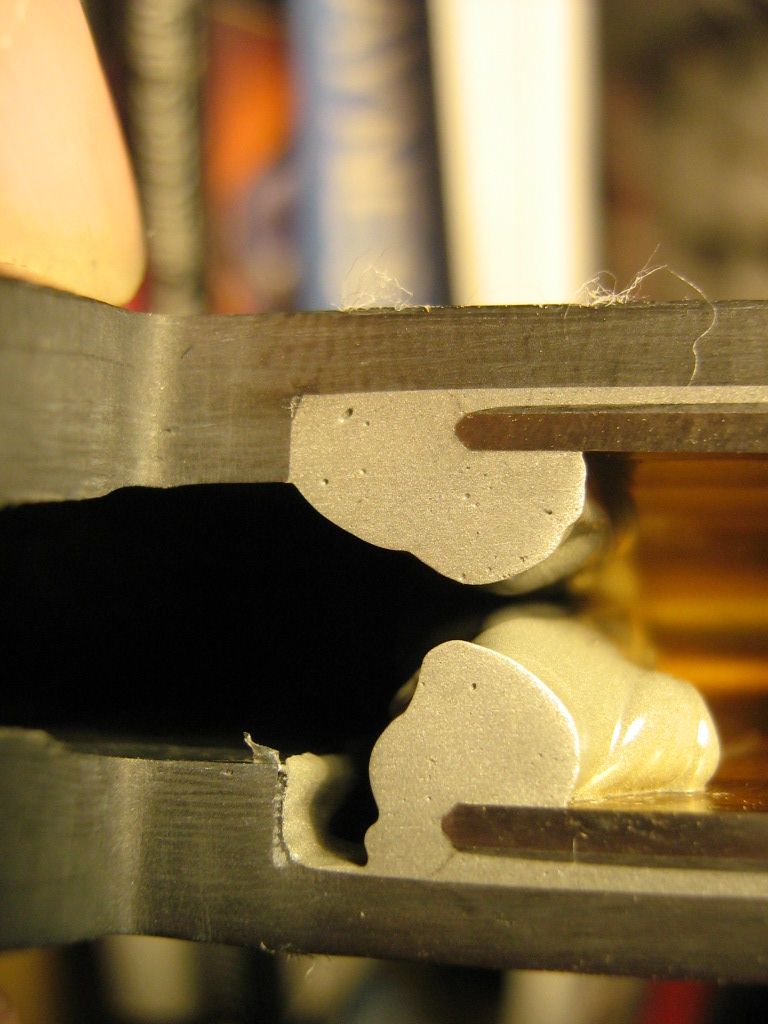
The fixings removed from the non-polished half. Washers omitted,

And now onto a few macro shots of the CF lay-up at different points.
The narrow splicing strips can be seen clearly at both the leading, and trailing edge locations.







Where both start to converge,

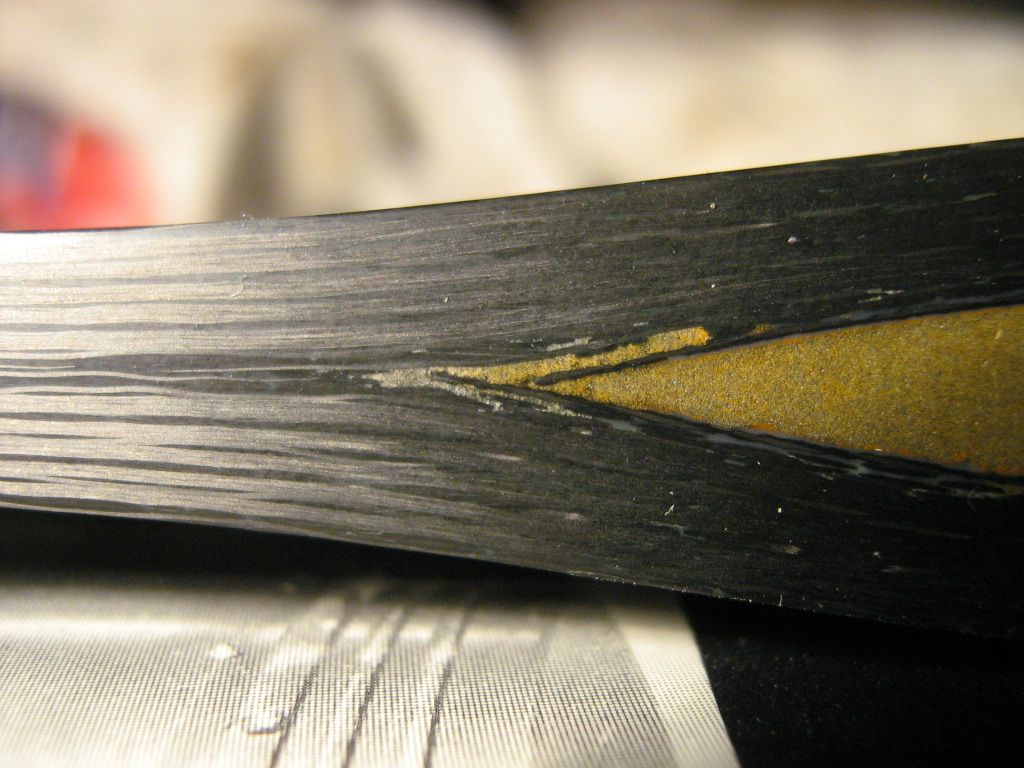
And last, the area surrounding single ti ferrule and washer(removed)

So, there you have it. Another extremely good learning tool for looking at.
What you see here should answer a lot of questions depending on what you want to make some day, it certainly did for me.
A day where you don't learn something new, is a day wasted.
Brian Garvey.