...you need to have depth to parts too... XX mm for example... (by looking at f1 cars).
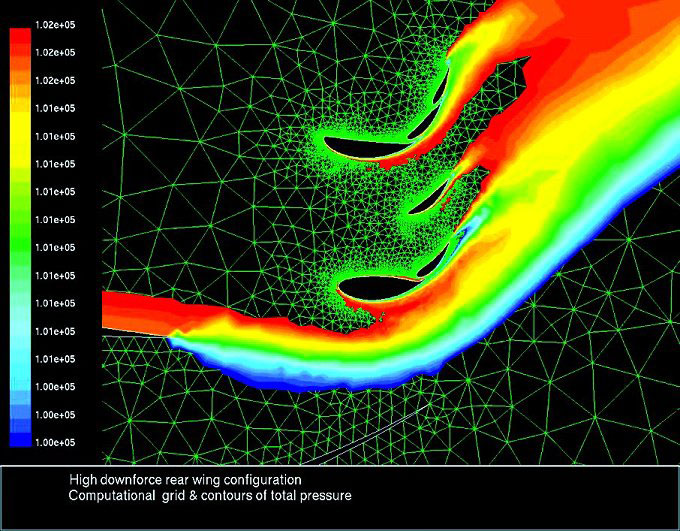
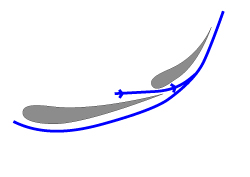
These Kashmin threads are feeding us some unoptimized designs, which are good food for thought.
So, to the point: Aerofoils are rounded in the leading edge and sharp in the back. At the back it is important to help the two flows merge smoothly, while at the front it doesn't matter too much since the obstacle the the airflow and the resulting stagnant high pressure area will force the air around an aerofoil shape anyways, so it is better to guide it like that (or at least that is my understanding).
But: do we really need a rounded leading edge? Wouldn't it be better to have an infinitely thin wing (not just at the edges, but along the whole span), to reduce the leading edge pressure buildup? Is the roundness just the consequence of the aerofoil needing a minimum rigidity in real life to keep its shape and support the load? Would an infinitely thin foil made of flattened unobtanium (with an optimized shape) perform better than its actual chubby incarnations?
I suspect the answer is not, but why not? Is denying the air some otherwise available volume helping generate downforce (lift in planes)?