http://www.motorsport.com/f1/news/bite- ... ls-735720/
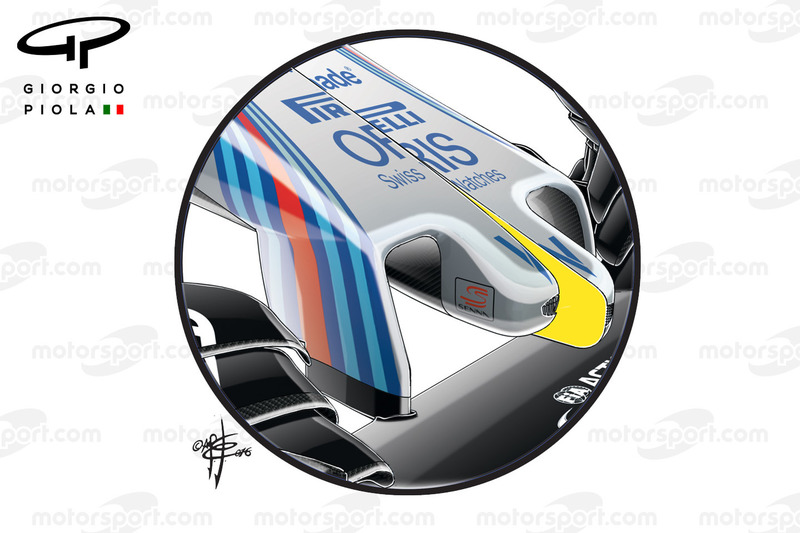
It's pretty common knowledge here in the paddock that they 3D print a large amount of the rear including the G/Box. I believe its done in Alsi9Cu3 alloy and In718 (Nickel Alloy - High temp metal).LookBackTime wrote:from ScarbsTech - Elegant Williams suspension bracket :
for me looks like is 3D printed - any opinion?
https://pbs.twimg.com/media/CiRd_VJWwAAwbGs.jpg:large
Which parts of the gbox are rapid prototyped? surely none of the loaded internals are viable. Did you mean the outer casing?Reckoner wrote:It's pretty common knowledge here in the paddock that they 3D print a large amount of the rear including the G/Box. I believe its done in Alsi9Cu3 alloy and In718 (Nickel Alloy - High temp metal).LookBackTime wrote:from ScarbsTech - Elegant Williams suspension bracket :
for me looks like is 3D printed - any opinion?
https://pbs.twimg.com/media/CiRd_VJWwAAwbGs.jpg:large
I believe all outer casing including suspension pick up points. Internal wise oil gallery components and major drive lines. The actual cogs are processed in a different manner but they have nearly cracked it where by they can 3D print the whole thing. Incredible stuff.Pierce89 wrote:Which parts of the gbox are rapid prototyped? surely none of the loaded internals are viable. Did you mean the outer casing?Reckoner wrote:It's pretty common knowledge here in the paddock that they 3D print a large amount of the rear including the G/Box. I believe its done in Alsi9Cu3 alloy and In718 (Nickel Alloy - High temp metal).LookBackTime wrote:from ScarbsTech - Elegant Williams suspension bracket :
for me looks like is 3D printed - any opinion?
https://pbs.twimg.com/media/CiRd_VJWwAAwbGs.jpg:large
There is no reason they wouldn't be able to manufacture the whole thing using additive methods right now, however there is no need to. Gears, shafts, bearings etc. are either easier, cheaper and quicker to manufacture using traditional means or source-able from an external company. Additive manufacturing makes no sense for these parts.Reckoner wrote:I believe all outer casing including suspension pick up points. Internal wise oil gallery components and major drive lines. The actual cogs are processed in a different manner but they have nearly cracked it where by they can 3D print the whole thing. Incredible stuff.Pierce89 wrote:Which parts of the gbox are rapid prototyped? surely none of the loaded internals are viable. Did you mean the outer casing?Reckoner wrote:
It's pretty common knowledge here in the paddock that they 3D print a large amount of the rear including the G/Box. I believe its done in Alsi9Cu3 alloy and In718 (Nickel Alloy - High temp metal).
Having been to xtrac, a leading gearbox manufacturer for F1 and motorsport and having research extensively I can tell you that none of the gearbox is manufactured from 3D printing. Gears and shafts are all manufactured using milling techniques and casing are made from either sand or investment casting. I imagine the only time 3D printing is used is to evaluate prototype parts for future designs. ALthough Williams manufacture their own gearboxes and not xtrac I see no reason why they would opt for 3D printing which is far more expensive and significantly slower than conventional manufacturing techniques.3jawchuck wrote:There is no reason they wouldn't be able to manufacture the whole thing using additive methods right now, however there is no need to. Gears, shafts, bearings etc. are either easier, cheaper and quicker to manufacture using traditional means or source-able from an external company. Additive manufacturing makes no sense for these parts.Reckoner wrote:I believe all outer casing including suspension pick up points. Internal wise oil gallery components and major drive lines. The actual cogs are processed in a different manner but they have nearly cracked it where by they can 3D print the whole thing. Incredible stuff.Pierce89 wrote: Which parts of the gbox are rapid prototyped? surely none of the loaded internals are viable. Did you mean the outer casing?