Dipesh1995 wrote: ↑01 Aug 2017, 12:05
Ok so convergence of Tke has significantly improved, my Y+ is still high around some areas. I've also lost a significant amount of downforce (3506N) but also drag (264N) so L/D has increased.
I also ran it with SST however it became very unstable , I'm guessing because SST doesn't work very well with high Y+.
Yeah, so because of your cell count restrictions, we're aiming for a higher y+ with a different turbulence model - so yeah SST would become unreliable at best.
It is good that your Tke has improved - from the looks of the residual plot, there was still a downward trend in the residuals... It is probably worthwhile running for 1500-2000 iterations, at least once, so that you can get a good 300ish steps at the fully converged state. Because you are running a RANS simulation, the results that you get are kinda meant to be interpreted as something like "the
average flow path (or movement etc.), that the fluid follows over an infinite time"... basically, you will miss any transient or unsteady behaviour, because you are taking the fluctuations that each cell experiences over the total number of iterations, and then averaging them to get ONE value. So a good thing to do at first, is to run the results for an extra 300-500 iterations past the point you define as them being converged, and then grab all 500 force values from those iterations and just do an average (in excel or something), and that is "technically" more accurate than taking the final value of the simulation, because at that iteration, you may be at the peak of an oscillation or something.
As a "general rule of thumb";
- A decrease in residuals by three orders of magnitude (10^-3) indicates at least qualitative convergence. At this point, the major flow features should be established.
- Species residuals may need to decrease to 10^-5 in order to achieve species balance.
- Energy residuals should decrease to at least 10^-6 (for a pressure-based solver).
Where the y+ is still quite high, I would suggest decreasing the minimum size of the prism layer cells, because not only will that hopefully help with the overall y+ distribution, but it would allow for smaller cells to be used at the leading and trailing edges of each aerofoil. At the moment, the y+ in those regions is within the buffer region, and so they no longer follow the viscous sub-layer theory, nor the log-law, and so cannot be accurately predicted. The leading and trailing edges are arguably, the most important bit of an aerofoil to capture. I would set your surface wrapper cell size on the aerofoils to something like 1.0mm, and then set your minimum prism layer cell size to be around 0.5mm. I would then also suggest making the refinement boxes you have around the leading and trailing edges a teeny bit further forward and backward respectively, and then reduce the cell size within there to maybe 50% what it is now (70% if cell count is an issue after the previous suggestion). You could also try increasing the surface curvature setting a little more too. If that still doesn't fix it, you can then increase your layer count to somewhere between 8-14 pretty safely, but the higher you go trying to "fix" the y+, the more likely it is that a different setting needs to be changed first
.
.
.
.
.
Dipesh1995 wrote: ↑01 Aug 2017, 19:44
One question I had was, since I'll be starting to design the complex wing Mk2 soon, would trimmer be suitable mesh to use over polyhedral mesh for a complex design? One of the key benefits I saw switching from polyhedral mesh to trimmer mesh was the lack of computational time required to generate the mesh.
To give you a general idea of the differences, the trimmer meshing method is more efficient for filling large volumes (i.e. the big size of the computational domain for a motorsport CFD analysis) and uses less memory per cell because it has less cell face/boundaries that it needs to keep track of throughout the simulation, however, it means that your total cell count will increase. The polyhedral mesher is more suited to complex geometries, and multi-region problems, and it converges quicker (and more reliably) than trimmer meshes usually do; however, because some of the polyhedra that the mesher creates sometimes have 20+ faces, it means that it is quite memory intensive to keep track of all those boundaries. The meshing process (depending on software) can also take longer for polyhedral as some software packages (such as ANSYS FLUENT - CFX doesn't offer polyhedral) will first mesh a fully hex-tetrahedal (cube) mesh, and then perform another meshing pass to "convert" that hex-tet into a polyhedral one. When used correctly, it can kind of allow your setup to be a little less rigorous given its affinity to complex shapes etc, however, use with caution

That comment is not a get out of jail free card!!
The pictures here show you that the polyhedral looks like it has fewer cells etc, however, you can still see that the size difference between the ones at the leading and trailing edges of the aerofoils vs. the larger main fluid domain cells is still a few orders of magnitude.
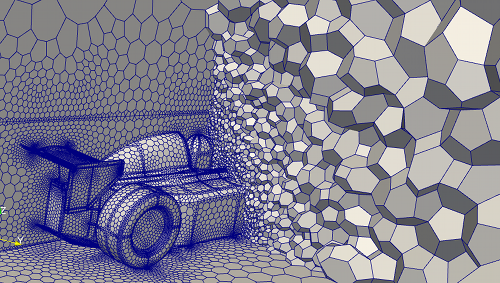
.
.
.
.
.
Dipesh1995 wrote: ↑01 Aug 2017, 19:44
Yeah so since this wing is not meant to be used on one my cars as such, I'll do the mesh sensitivity study using a similar mesh for one of my Formula Student car front wings. I must say I really do appreciate the help you and Vyssion have given me in sorting my CFD issues.
No worries mate - We love this stuff
