You write:
“but what does the tilting valve bring to the table? Asymmetric timing and if so, in which direction - late?”
In theory the tilting valve enables a different control over the gas flow.
The scavenging starts with a higher pressure just before the transfer ports (outside the cylinder).
At the beginning of the scavenging the fresh gas bursts into the cylinder (which enables an earlier opening of the transfer relative to the opening of the exhaust; the transfer port opens after the exhaust port).
The scavenging starts “positive”: from the opening of the transfer port to the BDC (Bottom Dead Center), the piston (with the tilting valve sealing its back end, and due to the small dead volume in the scavenge pump) displaces the air-fuel mixture into the cylinder positively (it resembles with the exhaust cycle of the 4-stroke engines: no matter what the pressure in the exhaust manifold is, the piston will push positively the burnt gas outside the cylinder).
Things change near the BDC wherein the tilting valve opens.
Now the space inside the piston (i.e. the “crankcase” of the OPRE Tilting) is free to communicate with the cylinder through the open scavenge port, and the scavenging turns from “positive” to “inertial”.
With the inertia of the fast moving gas “column” in the transfer - cylinder - exhaust, the transfer continuous strong till the closing of the transfer port, sucking gas from the space inside the piston and the inlet port.
At the end of the transfer, with the flow of the fresh gas from inside the piston towards the “scavenge pump” (and from the inlet port towards the space inside the piston) already strong, the filling (or overfilling) of the scavenge pump space with fresh gas continues uninterrupted till the closing of the tilting valve near the TDC. After the TDC the already established flow of fresh gas from the inlet port into the “crankcase” continues uninterrupted, while at the same time the gas trapped into the scavenge pump undergoes a compression by the outwards moving piston.
The bigger the tilting valves, the better the breathing at high revs.
The over-square design enables bigger tilting valves to be used (look at the openings between the tilting valve and the back end of the piston):
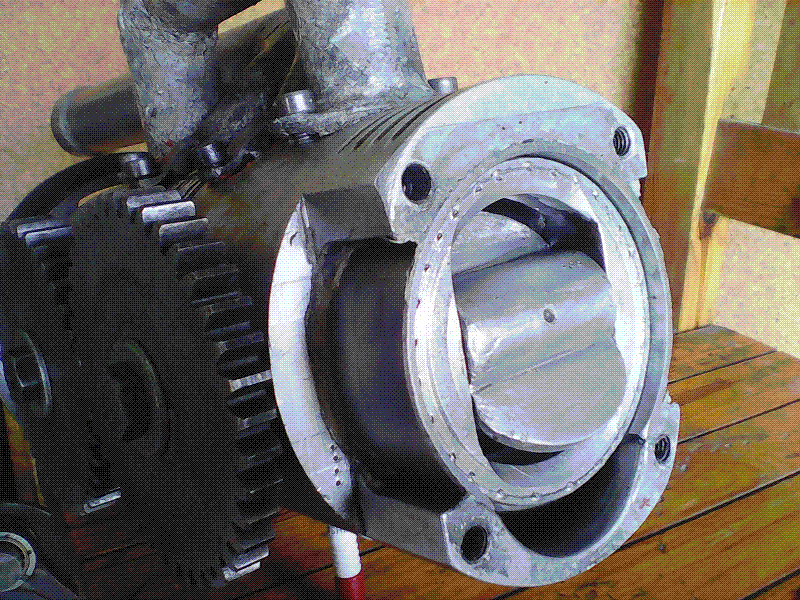
In the prototype (Opposed Piston) there are two big tilting valves (one per piston), each serving 333/2=166cc of cylinder capacity.
The over-over-square design (84mm bore for 30mm piston stroke in the prototype) besides enabling big tilting valves it is also enabling a “cross” (not loop) scavenging (you can call it cross uniflow) that prevents the mixing of the burnt gas with the fresh gas (say, similar to the through scavenging along the cylinder axis of the Junkers Opposed Piston Air engines).
The pulling-rods is another parameter which relates with the tilting valves: around the BDC the gas and the scavenging feels as working into an engine running at, say, 30% higher revs, which augments anything related with the inertia of the gas.
Regarding the “asymmetry”:
While geometrically the transfer and the exhaust are symmetrical, in practice the transfer appears strongly asymmetrical because it starts true positive (at the expense of some energy for the compression of the gas in the scavenge pump) and continues inertial after the BDC.
The intake is heavily asymmetrical (the inlet port is permanently open, the tilting valve makes the difference).
In practice:
Without reed valves it is saved bulk, weight, cost, noise and problems (what is omitted cannot fail).
The tilting valves (which are nothing but extensions of the connecting rods at their small ends) is reliable, adds no weight, makes easier the lubrication of the wrist pin, etc.
With one only prototype of worse than bad manufacturing quality, the timing used and the dyno test are meaningless. The carburetor used is inappropriate. The spark advance is constant.
With such an attenuated (bad) combustion chamber (worse than Wankel rotary) and the spark plug on the cylinder liner, it should misfire, at least. Yet, the prototype runs without misfiring.
The next cylinder is going to have this combustion chamber:
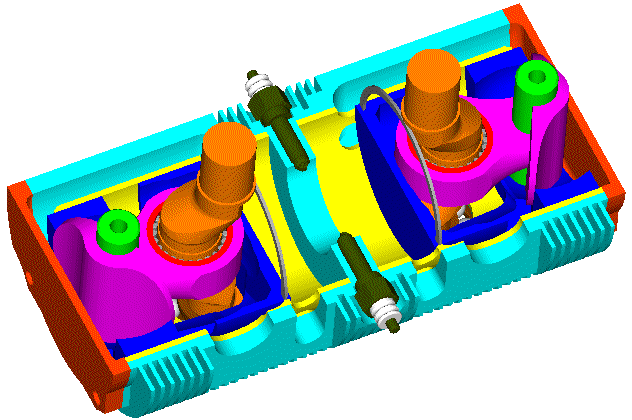
with spark plugs near its center and strong squeeze; the cross uniflow scavenging is not at all affected by the central narrowing of the cylinder.
The purpose of the OPRE Tilting engine is to power the Portable Flyer (as it is filed in the GoFly / Boeing competition at http://www.pattakon.com/GoFly/index.html ).
Theoretically, at least, for the high revs it is to work permanently . . .
Thanks
Manolis Pattakos