It will depend on your damper design and the max. bump/compression damping forces you want to achieve.DEFOE wrote: 1.how many gas should be filled in shock absorber?and the relations between sealing。
As an guide line, you can use this formula:

for your damper (assuming a 45mm piston) this would make:

This would be more or less the "worse case" but it will be save, and limiting the risk of cavitation.
But to answer this question more acurate, we would need to know a little bit more about your damper design.
Is it a monotube or twintube damper, does the damper has a valve or restriction inbetween the oil in the compression chamber and the separation piston, or does the separation piston sees the full pressure in the compression chamber?
The formula above is for the case that the separation piston sees the full oil pressure in compression/bump.
Such designs include for example: typical Bilstein dampers,some TEIN, KONI, some SACHS, ÖHLINS and Penske designs, most "cheap" monotube dampers such as AFCO and others.
The internals would look like this:

or this:

In this case the separation piston will need to support all the pressure in the compression chamber.
With high damping forces in compression/bump direction this dampers will need very high internal gaspressue.
Normal values for these types of dampers are ~20-25 bar.
This damper design is not very suitable for large diameter shafts, as the gasforce, preload or "nosepressures" will be very high.
This is one of the main reasons, that you normally see BILSTEIN dampers with small 10-12 mm shafts.
If the gaspressure is too low, the separation piston will move on impact (shockwave) more then the shaft, this leads to an increase in internal volume and therefore a pressure drop in the oilcamber (rebound side), this can lead to possible cavitation inside the damper.
See the following illustrations:
correct pressure:
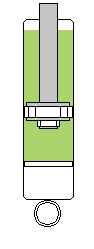
gaspressure too low:
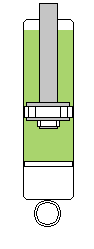
If your damper has a valve or restriction (orfice) between the volume of the compression chamber and the separation piston, then you can run lower pressures.
The principle of such a damper will look like this.

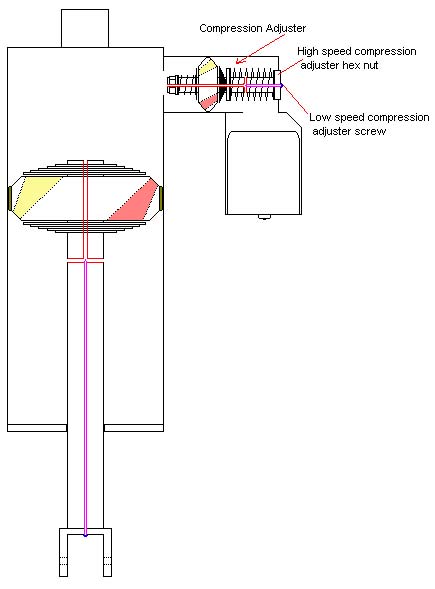
Most monotube racing dampers with external canisters/reservoirs will work like this. (for example Penske,Proflex or SACHS RDS dampers etc.)
As the valve will create a pressure drop between the oil in the compression chamber and the oil in front of the separation piston, the pressure which acts on the separation piston will be lower.
Therefore less gas pressure is needed to suppot the piston.
How much less will depent on the pressure drop at the valve, and will change with the settings if the valve is adjustable.
One would need to do a calculation when the valve design in question is know, it´s difficult to make an "rule of thumb" statement, but such dampers normally use 10-20 bar of pressure, with 12-16 bar beeing a common value for most of them.
If you use a value calculated by the formula above, you will be on the "safe side" as far as cavitation goes, but will need to live with increased friction, hysteresis (caused by the gas spring effect) and preload/gasforce especially if large shafts are used.
How much of an problem this is, will depend on your application and the spring rates used.